The Eminence Factory
The first Eminence facility, located in downtown Eminence, was less than 6,000 sq. ft. and employed around thirty people. In 1972 Eminence Speaker moved to a new location in Shawnee Industrial Park on Mulberry Pike where we remain today. The facility has seen several additions. The first building in this location was just less than 30,000 sq. ft., but now has grown to include nearly 100,000 sq. ft. all under one roof.
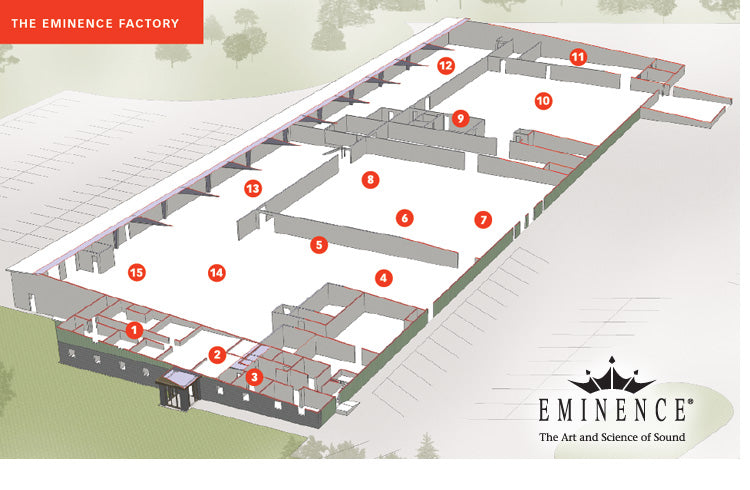
1 - Engineering
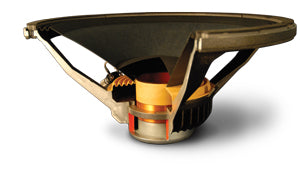
The product development process begins here, with a request that is initiated by a customer. Eminence engineers diligently work to satisfy the needs of individual customers through a custom design, or to assist in the integration of an off-the-shelf Eminence product for their application. Our engineers incorporate the use of multiple technologies such as Finite Element Analysis, 3D CAD systems, CNC machining, and computerized test equipment to verify designs. Our fused deposition modeling rapid prototype machine enables us to quickly develop parts for the sampling process, which has helped our engineers produce as many as 2,000 hand-built samples per year.
2 - Sales & Customer Service
All sales for our custom OEM and Eminence branded products are administered here. We pride ourselves on our customer service, and have built a reputation within our industry for providing the highest quality products and support. Our 7-year warranty says it all.
3 - Management / Administration
This area houses Accounting, Production Scheduling, Marketing, Purchasing and Executive Management.

4 - Voice Coil Department
Eminence has developed the finest voice coils in the industry. We currently produce 1 layer edgewound, 2 layer, 4 layer, and dual 2 layer coils. Winding lengths vary from .210 (5.3mm) to 1.25 (31.75mm). Standard impedances range from less than 1 ohm all the way to 32 ohms.
5 - High Frequency Department
Eminence offers HF products for both our branded and OEM product lines. Products include several 1 throat devices, some incorporating neodymium motor structures, and others with standard ferrite motor structures. Eminence also offers a larger 2 throat HF device.
6 - Warehouse
Inventory of all Genuine Eminence finished goods is stored here.
7 - Receiving / Q.C.
Incoming components are received in this area and go through a rigorous Q.C. evaluation process. We believe quality products can only be made from quality components.

8 - Component Storage
Many of our components, including cones, gaskets and packaging are stored here.
9 - Dust Cap Department
We have the capability to produce custom-logo dust caps, incorporating the use of pad printing, decal transfer or hot stamping.
10 - Press Shop
We are well known for manufacturing a wide array of products while minimizing the number of outsourced components. Our Press Shop allows us to make all our top plates and back plates, as well as the ability to modify many purchased components. The Eminence Press Shop houses 13 presses, including three 300-ton Verson presses and one 600-ton Multipress.
11 - Tool Room
The machinery and technology used in the assembly of loudspeakers is not something readily available from your local hardware store. The Eminence Tool Room designs and manufactures most of the tools and equipment used in our daily manufacturing activity. The efforts of this department represent some of the industrys most significant advancements in loudspeaker production.
12 - Paint Department
Eminence uses a state-of-the-art electrocoat paint system just like the leading automotive and appliance manufacturers. With this system we can apply a uniform coating of cationic epoxy paint over the entire surface of our metal parts, including the magnetic gap, to a controlled thickness of less than 0.001.
13 - Final Assembly
The Eminence Final Assembly process is based on an integration of human elements along with the finest assembly machines and tooling available in this industry. There is no substitute for conscientious assembly technicians involved in the manufacturing ofour products.
14 - Testing / Packing Department
All products move from Final Assembly to our Testing/Packing Department where they are carefully inspected. After cosmetic amendments are added, they are packaged for shipment throughoutthe world.
15 - Shipping / Finished Goods
Most products we produce on a custom basis go from Testing/Packing to Shipping and are quickly dispatched to respective customers. **Canada Customs requires Canadian recipients to pay applicable duties and taxes on each shipment entering Canada. These charges may include PST, GST, HST, duties and other taxes of goods (e.g. excise tax). A brokerage fee is also charged to process shipments and present the requisite customs paperwork to Canada customs on the importer's behalf.